생산 현장에 도입…작업자 편의·안정성 확보
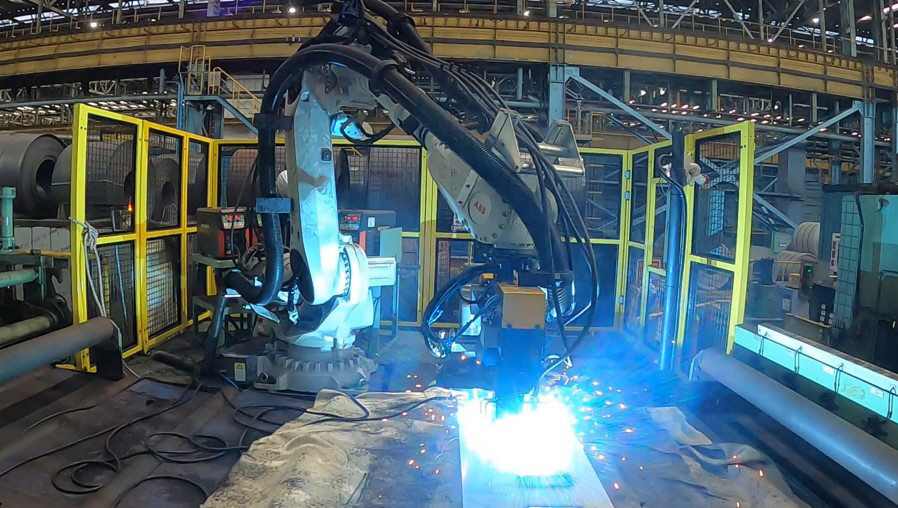
지난 1999년부터 산업용 로봇을 도입하기 시작한 포항제철소는 올해만 8대를 추가도입하면서 현재 90여대의 로봇을 운영중이다.
특히 그동안 비정형작업이 많은 철강 생산 공정 특성상 시료 이송 등 단순 작업에만 주로 도입됐지만 최근 스마트 기술을 활용하면서 다양한 생산 현장에 자동화 로봇을 도입, 작업자의 안전 확보 및 편의 증대는 물론 생산성과 효율성까지 높이고 있다.
대표적인 로봇은 전기강판공장을 비롯한 압연 공정에서 사용되는 ‘슬리브 인출 자동화 로봇’이다.
슬리브란 코일제품의 중앙에 들어가는 심으로, 철판을 원통형태로 감아주거나 풀어주는 과정에서 코일의 형태를 유지해 주는 역할을 한다.
그동안 포항제철소는 코일을 감기 전 슬리브를 설비에 장착하거나 코일을 푼 뒤 남아있는 슬리브 제거는 온전히 작업자에 의해 이뤄졌다.
특히 철이나 고무로 만들어진 슬리브는 기계를 이용해 장착 또는 제거하지만 종이재질의 경우 15㎏~20㎏에 달하는 슬리브를 작업자가 직접 장착·제거해야 돼 근골격에 큰 부담을 줘 왔다.
슬리브 인출 자동화 로봇은 이 같은 문제를 완전히 해결, 작업자의 피로부담을 덜어주는 것은 물론 설비 부근에서 작업 부담까지 줄여 안전확보까지 가능해졌다.
현장 관계자는 “몸에 부담되는 작업을 로봇이 대신 해주니 편하고, 다른 작업에 집중할 수 있어 업무 효율도 높아졌다”고 말했다.
또 STS 소둔 산세 공장에는 ‘덧대기 용접 자동화 로봇’ 테스트가 한창이다.
소둔산세 공장은 스테인리스 스틸 제품 품질 확보를 위한 열처리와 세척을 담당하는 곳으로, 두꺼운 고합금 스테인리스 스틸 소재 처리 과정에서 코일이 끊어지는 판파단 현상이 발생하기도 한다.
판파단 현상이 발생하면 설비 손상은 물론 생산 라인이 멈추게 돼 생산성 저하의 원인이 된다.
이 때문에 소둔 공정에서는 설비를 이용한 1차 용접 후 보강용 시편을 덧대는 ‘덧대기 용접’을 해야하지만 수작업으로만 가능해 안전 사고 위험은 물론 매 공정마다 작업자가 용접을 해야 하는 번거로움이 있었다.
포항제철소는 이를 해소하기 위해 최근 ‘덧대기 용접 자동화 로봇’을 도입해 테스트에 들어갔다.
이 로봇이 현장에 투입되면 작업자의 안전 강화는 물론 용접 시간도 수작업 대비 절반으로 줄일 수 있어 효율성을 극대화할 수 있다.
포항제철소는 생산 효율을 높일 뿐만 아니라 현장 안전을 강화하기 위한 자동화 설비도 확대한다.
실제 올해 도입한 8대의 로봇 중 절반 이상이 작업자 안전확보에 목적을 뒀다.
포항제철소 관계자는 “자동화 로봇을 이용하면 수작업을 대체할 수 있어 작업 환경 안전을 강화할 수 있다”며 “생산 효율 제고·품질 향상 뿐만 아니라 작업자의 안전과 편의를 높일 수 있는 자동화 로봇을 적극적으로 도입할 계획”이라고 밝혔다.